Preparing for Hurricane Season: 3 Problems and Solutions
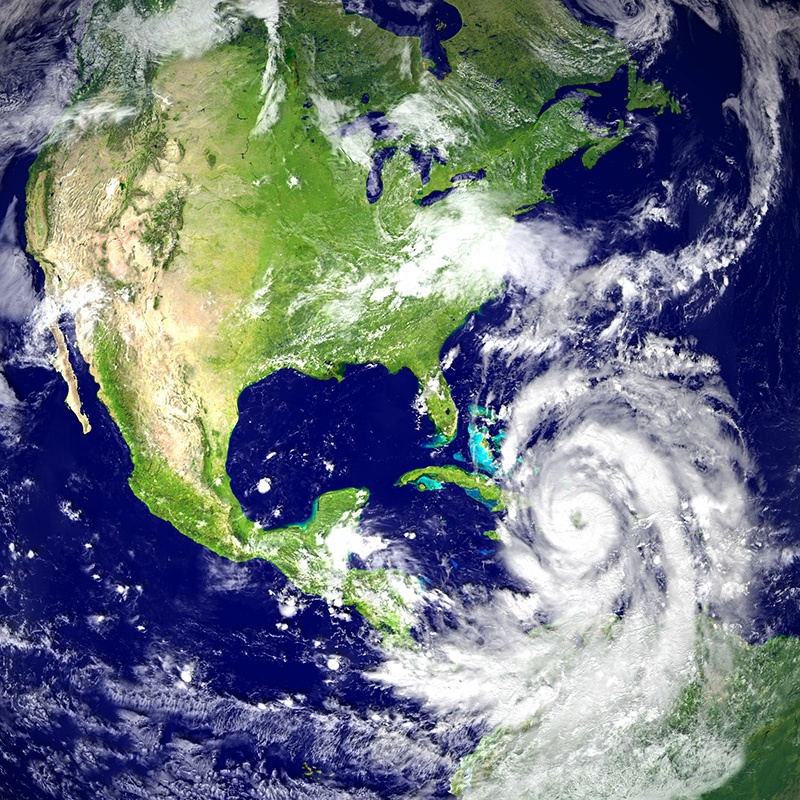
With areas of the Gulf Coast and Puerto Rico still recovering from the devastation caused by Hurricanes Harvey and Maria in 2017, it may seem too early to even be thinking about the 2018 Atlantic hurricane season. But the truth of the matter is, it’s never too early to be thinking about — and preparing for — hurricane season.
The official Atlantic hurricane season began on June 1st and runs until November 30th, with its peak typically early August through the end of October. On May 24th, the National Oceanic and Atmospheric Administration (NOAA) Climate Predicting Center released its annual forecast for the Atlantic hurricane season, and here’s what they’re predicting for 2018:
- Nearly as active a season as 2017, which was one of the most active on record.
- Most likely the season will be near normal or a little more intense than normal, with 35% probability above-normal, 40% near–normal and 25% below-normal.
- 10 to 16 named storms with sustained winds of 39 mph or higher.
- 5 to 9 hurricanes with winds of 74 mph or higher, with 1 to 4 of those expected to be major hurricanes — Category 3 (sustained winds of 111-130 mph) or stronger.
- Chance of an El Nino developing in late summer, which could weaken toward the end of the hurricane season.
No Time Like the Present to Get Prepared
We have all seen the damage on news reports from Tropical Storm Alberto which hit Florida over Memorial Day weekend. Its remnants have since caused scattered and severe flash flooding, downed trees and weather-related deaths throughout the Southeast, the Tennessee Valley and parts of Maryland.
As devastating and damaging as Alberto was, think of it as the calm before the storm — meaning, if the predictions from the NOAA regarding Atlantic hurricane season are on target, Alberto was nothing compared to what could be coming in the months ahead.
The lesson from Alberto is this…now is the time to be proactive and get your fleet operations prepared for hurricane season. That way, if and when a hurricane hits, you’ll have what’s needed in place to keep damages minimized, production maximized and your workforce safe and protected.
To that end, let’s look at three areas where a hurricane can cause problems for your fleet operations— fuel, workforce and vehicles — and what you can do to keep these problems minimized or, in a best-case scenario, have them not be a problem at all.
PROBLEM: No electricity, so fuel pumps are inoperable and fuel is unavailable.
SOLUTION:
- Make sure your contract with your fuel provider states that they must make a good faith effort to supply fuel when conventional fueling is not available.
- Have an emergency fueling plan in place. Cover, with your provider, the emergency services offered, how and when fuel will be delivered, the timeframe in which it will be delivered, the extent and security of their fuel networks, their tank wagon or fuel truck capacity and if an emergency point-of-contact is available 24/7.
- Keep vehicles topped off at all times, and have a minimum 72-hour emergency fuel reserve, which is the average time before a FEMA response.
PROBLEM: No one really knows what to do, and there is a state of chaos throughout the workforce.
SOLUTION:
- Have a disaster plan in place, and make sure that everyone knows proper procedure and expectations, including fleet mission and duties. Create a disaster organizational chart that clarifies individual responsibilities and roles, reporting procedures and steps for 24/7 operations.
- Conduct dry runs of the disaster plan to ensure it’s working as expected and tweak where necessary.
- Establish methods of communication for employees, such as Facebook or group text messaging, and share employee contact information to keep everyone in the loop.
- Time is of the essence, so map out evacuation or emergency routes for drivers and other employees, and make sure they are familiar with those routes. If vehicles need to be relocated, inform drivers in advance of the location and, if needed, make arrangements for drivers to return to home base.
- Keep employee emergency skills up to date. Include basic first aid, CPR, search and rescue techniques. Conduct training drills or tabletop exercises with specific objectives.
PROBLEM: Vehicles are not road-ready (due to dead batteries, flat tires, water in cabs, exterior damage, such as smashed windshields, etc.) and, therefore, production is suffering.
SOLUTION:
- If maintenance is performed in-house, make sure you have a generous supply of parts and tools on hand to fix whatever is necessary.
- Conduct regular maintenance checks to help ensure optimal vehicle performance and maximum vehicle availability.
- If maintenance is outsourced, look over the steps your provider has in place, to ensure your vehicles will be reliably serviced when disaster strikes and that they will be back on the road as quickly as possible.
- If vehicles are parked outside, park them against the building and as close to each other as possible to protect the interior vehicles from flying debris.
- Remove any contents from the vehicles that could become projectiles (such as buckets, ladders or other equipment) and damage other vehicles.
Are you adequately prepared should disaster strike?
Get our "Preparing Your Fleet for Disaster Checklist"