Avoiding a Breakdown: Coolant Best Practices
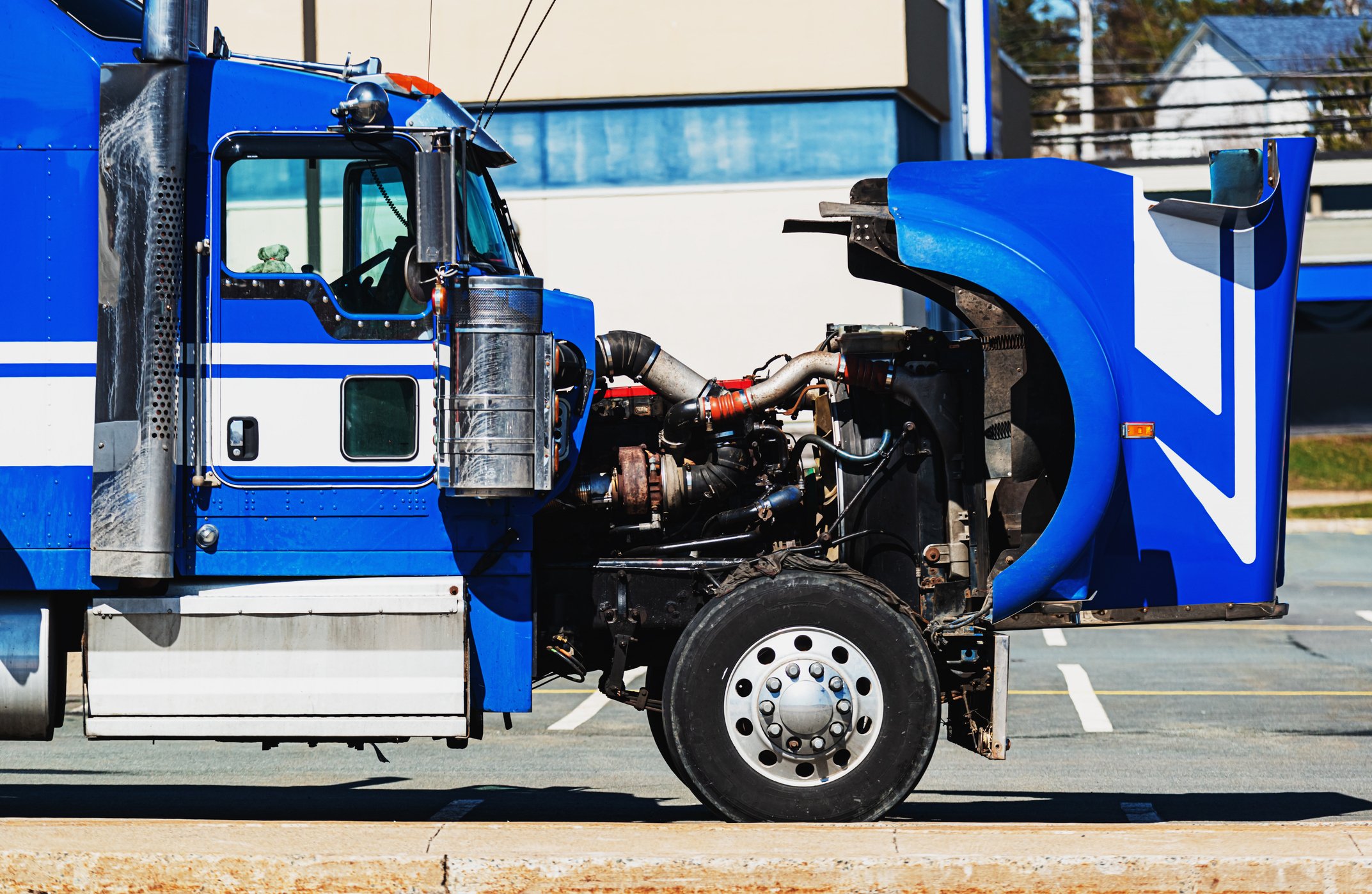
Routine maintenance tasks, including system inspections, tire rotations, oil changes, and fluid checks, are crucial to keeping your fleet running safely and efficiently.
While all maintenance tasks are equally important, there’s one that often takes a backseat even though 40% of on-highway breakdowns are attributed to it — engine coolant maintenance.
Coolant Maintenance: Essential for Vehicle and Fleet Efficiency
Coolant plays a critical role in regulating engine temperature. Its primary function is to protect the engine from overheating at high temperatures and freezing in cold temperatures. Additionally, it plays a crucial role in keeping metal surfaces in the radiator clean and protects against scaling, cavitation, and corrosion on engine components.
Neglecting coolant in your routine maintenance scheduling can have costly consequences. These include engine overheating, corrosion, radiator failure, and vehicle downtime — all of which can result in expensive repairs, unplanned downtime, and unhappy customers.
To prevent these bottom line busters from happening to your fleet, adopting and putting to use coolant best practices is essential to ensuring your coolant’s integrity and effectiveness and your fleet’s efficiency and productivity.
Let’s look at those.
Conduct Regular Testing and Inspections
To ensure coolant integrity, coolant testing is a top priority and should be conducted twice a year, ideally before summer and winter. Testing can involve sending samples to a lab or using test strips. If using test strips, ensure they match the coolant that’s tested.
Visual inspections are also helpful. Look for clarity and make sure that the coolant isn’t rust-colored. If an ammonia smell is present, it means the pH is out of balance and corrosion problems inside the engine are more likely to occur.
Before cold weather sets in, test your coolant’s freeze points using test strips. For optimal freeze point protection, maintain a 50/50 water/glycol mix.
Schedule Flushes
Over time, coolant loses its effectiveness due to the accumulation of contaminants and the breakdown of additives. Scheduling regular coolant flushes according to the manufacturer’s recommendations helps remove debris and replenish additives. This helps ensure optimal performance and longevity of the cooling system.
Go for Quality
Choosing the correct coolant is essential for maintaining optimal engine performance and longevity. All coolants are not created equal. And there are plenty to choose from that offer various abilities.
To simplify the selection process, coolants are available in different colors — typically green, red/pink, blue, and yellow. Coolant color can help you differentiate between coolants and determine what’s best for your needs, but it’s not 100% reliable. Different manufacturers may add dyes to their products for identification purposes, but these colors are not standardized across the industry.
Rather than relying solely on color, consult your supplier and discuss your requirements to ensure you’re using the compatible coolant type for your specific vehicle. Areas to cover include:
- The makes and models of the engines in your fleet
- Their OEM recommendations
- The maintenance goals you want to establish
Never choose a coolant based on price alone — you get what you pay for. To ensure effectiveness, you need to fully understand what you’re getting and why it’s best for your needs.
Pay Attention to Mixing and Dilution
When adding or replacing coolant, following the proper mixing and dilution ratios that are specified by the manufacturer is crucial. Improper ratios can cause reduced cooling efficiency, corrosion, and engine damage.
Address Leaks Promptly
Small coolant leaks can lead to big problems if they are not handled ASAP. Regularly inspecting vehicles for signs of leaks and addressing them will help prevent coolant loss and help protect the engine from potential damage, saving you time and money over the long run.
Educate Drivers
Drivers play a crucial role in identifying potential coolant issues such as leaks and should be trained on the steps to take before taking the vehicle to the shop.
Ideally, drivers should top off the coolant with the same coolant used by the fleet, so keeping an extra bottle on board is always a good idea. When a driver tops off the coolant, they should always let maintenance know. That way, maintenance knows to test the chemistry with test strips to ensure it’s still in balance.
Water is OK to use if coolant isn’t available, but not tap water. Tap water can cause scaling inside the engine, on the side of the radiator, or the heater core. Use deionized water or good-quality water only.
Stay on Top of Documentation and Record Keeping
Maintaining detailed records of your coolant maintenance activities — coolant flushes, inspections, repairs, and any other issues— will help with tracking performance and identifying trends over time. Analyzing this data will help you identify areas for improvement and ensure compliance with maintenance schedules.
Want more best practices for your fleet?
Download our Fleet Best Practices Guide today.