Water: The Enemy in Fuel Storage Tanks
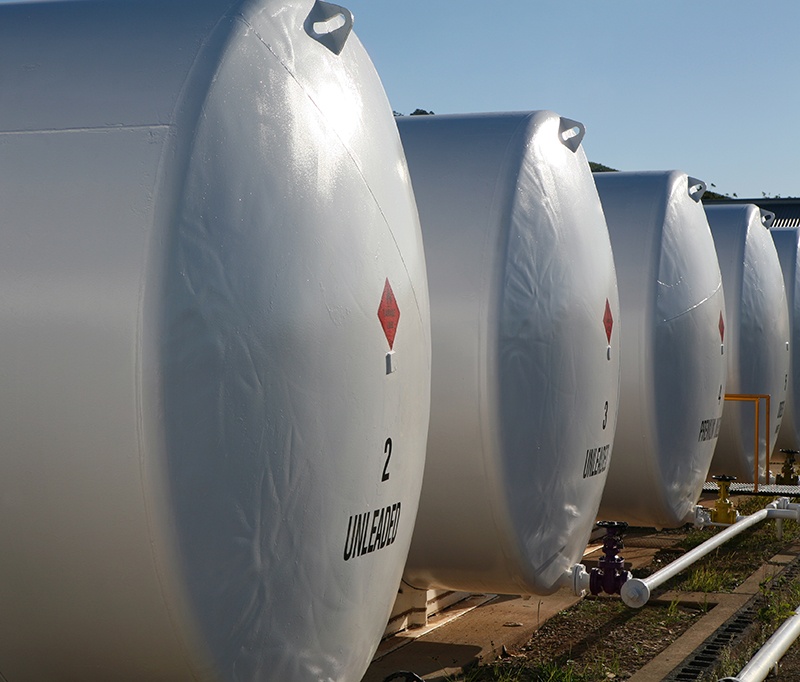
We all have heard the numerous health benefits of drinking water and many of us try diligently to get in the recommended eight glasses a day. But let your fuel storage tank take too many “gulps” of wondrous H2O and you have on hand—if not treated properly—a situation that can be very unhealthy for your bottom line.
Just as water and oil don’t mix, neither do water and fuel. Water accumulation can damage fuel quality, which in turn can cause problems that take a big bite out of business productivity and efficiency, including:
- Poor vehicle performance
- Failed exhaust emissions
- Major engine damage
- Plugged fuel filters
- Corrosion of metal parts of tanks and/or dispensing equipment
Controlling water accumulation in your fuel storage tank is critical and is one of the most important steps you can take to prevent budget busting problems from occurring down the road.
To that end, let’s take a closer look at how water sneaks its way into fuel tanks, how to prevent its accumulation, how to locate and remove it and how to check for microbial growth.
How Water Enters a Tank
Unfortunately, there are many ways that water can enter a fuel storage tank. It doesn’t matter if the tank is above ground or underground, what type of fuel product it is or from what material it is constructed. Some of the more common ways are:
- Water present in the delivered product
- Damaged spill bucket or fill cap gaskets, and loose fittings or plugs
- Allowing water captured in a spill bucket to be drained into the storage tank
- Condensation caused by air entering air vents or temperature swings
- Tank orifices that are not water/vapor tight
No matter how water finds its way into a tank, one thing is certain—it provides the perfect breeding ground for microbial bacteria to rapidly proliferate. With microbial growth, problems begin that could lead to microbial contamination and damage to the entire storage system.
Here’s how to help prevent that from happening:
Routine Maintenance
Protecting your fuel and your business from H2O accumulation woes, means staying ahead of the curve for potential problems. Follow these basic maintenance procedures on a regular basis and you’ll get the upper hand on this fuel enemy:
- Monitoring and checking for water with manual gauge sticks or with automatic tank gauging systems—this should be done as frequently as possible—even daily
- Inspecting fill and vapor caps for damage and missing gaskets and replacing if necessary
- Inspecting product and spill containment buckets and if water is found, disposing of it and not allowing it to drain back into the tank
- Auditing the fuel delivery process and water content
- Checking for signs of slowed fueling
- Using water-sensitive fuel filters
- Regularly treating tanks with antimicrobial pesticide
- Hiring a professional service to examine the inside of the tank and having it cleaned periodically
Locating Water and Removing It
Manual tank gauging or automatic tank gauging can detect if water is present, but perhaps the most effective method is pulling fuel samples on a regular basis. To get the best results, take samples from the low end of the tank and from more than one location.
If the samples are hazy or waxy looking, water is present and must be removed as soon as possible and not by you. Contacting a petroleum equipment or services contractor or your fuel supplier for guidance on removing water from the tank is the course of action to take.
Detecting Microbial Growth
Since microbial growth creates slime and sludge, plugged fuel filters and filters with a life span shorter than six months are common indicators of microbial growth. Other signs of microbial growth include a rotten egg smell, plugged fuel lines, erratic gauge readings and frequent replacement of valves, hoses and rubber seals.
Field detection kits can determine if microbial growth is present, but it is best to leave this to microbial contamination experts, so if growth is detected they can develop an effective treatment plan. This could involve a thorough tank cleaning to remove slime and sludge followed by treatment with a biocide.
PS Energy offers Telematics Software Solution that will allow you to track your fuel inventory remotely and from one location. Find out more about Etrac for your company.