How to Be Safe and Benefit from Aboveground Storage Tanks
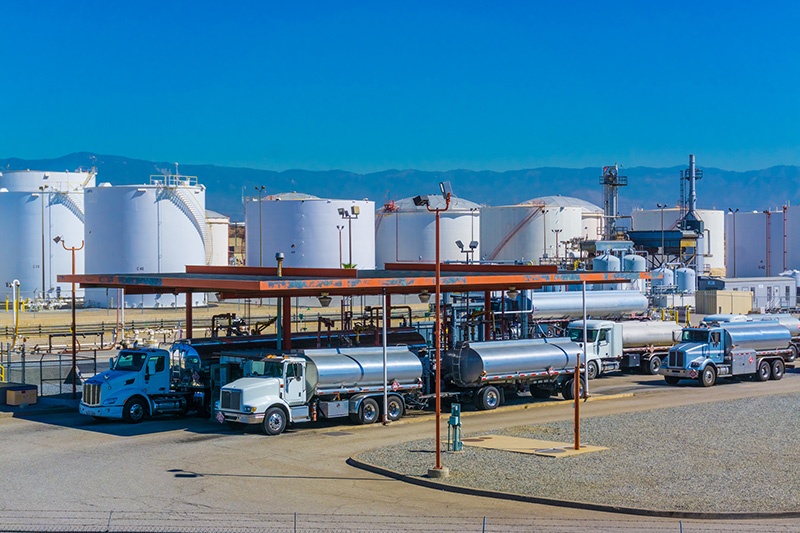
With innovations and technological advances in tank construction and also in fuel delivery, dispensing and monitoring, using aboveground storage tanks for fuel storage is safer than ever before, and if managed and maintained properly, they can provide fleets numerous advantages.
For example, there’s improved product security, a price break for buying fuel in bulk, greater control over inventory and the convenience of not having to wait on a fuel delivery service to top off vehicles or equipment—meaning less downtime, increased productivity and improved operating costs.
But, despite the advantages, aboveground storage tanks are not the best option for every fleet. There are important factors to consider, including annual fuel usage, annual fuel spend, the type of fuel utilized and whether fleet vehicles return to “base” regularly.
Further, aboveground storage tanks require compliance with federal, state and local regulations, and failure to do so could mean costly fines. What can also prove costly are inferior monitoring and safety practices—just one accident could wreck your bottom line.
Be Safety Savvy
While improvements have made aboveground storage tanks safer, the potential for risk is always there. Controlling your risks means following some common—and common sense—monitoring and safety best practices.
So, let’s take a closer look at a few of those.
1. Installing: Requirements for installation depend on the type of product stored. For example, if the product may present a fire hazard, the installation must comply with specific fire safety and design and installation specifications, most of which are sourced from the National Fire Protection Association (NFPA).
General aboveground storage tank installation guidelines from NFPA include:
- Tanks should be located on a high, well-drained site at least 40 feet (including fueling apron) from any building, water tributary or combustible materials.
- The storage area should be free of weeds and combustible materials, with open flames and smoking prohibited. “NO SMOKING” signs should be highly visible.
- Tanks should be installed in an east-west orientation to reduce the amount of solar radiation the tanks receive.
- Tanks should be clearly marked with the name of the fuel contents and have “FLAMMABLE-KEEP FIRE AND FLAME AWAY” signage in bright red, with letters at least six inches in height.
- Class B fire extinguishers should be mounted in locations where they can be easily accessed.
- Concrete or steel tank saddles are required by law, unless tanks in contact with the ground are protected against corrosion.
2. Contamination and Monitoring: Aboveground storage tanks should be routinely monitored and integrity tested to ensure there are no leaks, that the tank is in good working condition and that the tank is not at risk for failure due to corrosion or other factors.
If a tank is new, a system audit by an engineer is always a good idea, to identify and correct problems, including loose fittings, inferior welding and gaskets that are poorly fit.
And, while you are responsible for the quality of the fuel once it is in your tank, you can work with your fuel provider to keep deliveries clean. Also, be sure to ask your provider about a GPS system to monitor tanks. Monitoring will let you keep track of fuel levels, the time fuel is dispensed and alerts for when filters need to be changed.
3. Testing for Water: Water accumulation can damage fuel quality, leading to all kinds of problems down the road, including poor vehicle performance, failed exhaust emissions, major engine damage, plugged fuel filters and corrosion of metal parts of tanks and/or dispensing equipment.
Manual or automatic tank gauging can test for the presence of water, but the most effective method is pulling fuel samples on a regular basis—even daily.
For the best results, take samples from more than one location and from the low end of the tank. If the samples appear hazy or waxy looking, it means water is present and must be removed as soon as possible. For removal, the first action to take is to contact a petroleum equipment or services contractor or your fuel supplier for guidance. Never attempt to remove on your own.
4. Training: Managing the risks associated with aboveground storage tanks is essential, and employees who work on the equipment or around the fuel storage locations must be trained to identify and eliminate risks.
Employees should know how to conduct routine inspections of tanks, how to dispense fuel and operate pump shutoffs, how to contain and clean up spills and what action to take in any potential emergency situation.
Bottom Line: Employees who are not expertly trained in the operation of storage tanks and equipment should never be involved in the delivery, monitoring or dispensing of product from storage tanks. But, with the right training and a safety savvy approach, aboveground storage tanks can be an excellent option for fleets, with collaboration from their fuel provider.
If you're interested in expanding fuel management options, check out our comprehensive fuel management program.