The Endless Benefits of Engine Calibration
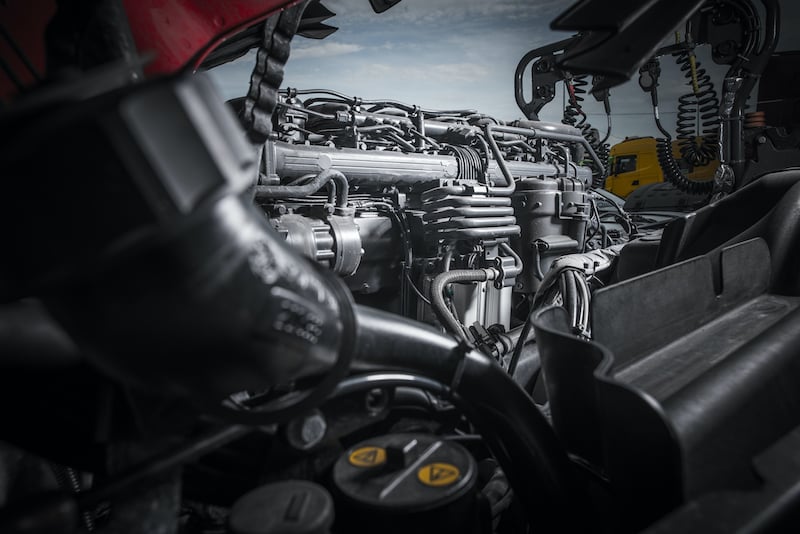
Because of the sluggish 2020 economy and its slowdown in business, fleet managers and owner-operators have had to develop cost-saving strategies to cut costs further and improve operational efficiency. Among those are focusing on vehicle utilization, renegotiating prices with vendors, and voluntarily reducing salaries.
While all are viable, someone should give another look to an overlooked strategy— engine calibration.
Engine calibration alters a vehicle’s engine parameters to align with the way the vehicle is used. The result is a vehicle working more cost-effectively and efficiently, which means lower fuel costs, improved safety, greater productivity, longer vehicle life, and a better bottom line.
Engine Calibration: A Look Under the Hood
Fleet vehicles accomplish a wide range of job-specific tasks, but mass-produced vehicles appeal to a wide range of buyers for various uses. To that end, when a vehicle is purchased, companies typically make alterations to that vehicle to align it with company needs. An example would be adding GPS/telematics systems, ladder racks, custom tires, and safety features such as strobe lights, reverse warning functionality, and light bars.
While any alterations are essential to a vehicle operating more cost-effectively and efficiently, engine calibration is an alteration that’s not often on top of a fleet manager or operator’s mind. With fuel costs, safety, and efficiency as top challenges, engine calibration is worth exploring.
Here’s how it works.
Engine calibration, which is performed by an engine calibration specialist after a thorough consultation on a fleet’s specific needs, is a process that adjusts a vehicle’s engine control module (ECM) by implementing customizations to the software coding that tells the engine how to run. These modifications refine engine parameters — such as allowable top speed, idle RPM, and shift points — to a vehicle’s specific need, thereby reducing fuel usage, protecting drivers, and minimizing fuel spend.
By using software, custom calibrations are installed into a handheld programmer that the specialist plugs into the vehicle OMD-II port. The specialist then optimizes the ECM settings with the software to implement the calibration. Drivers can’t operate the vehicle outside of the modified parameters. For example, if a parameter is at the maximum speed of 65 mph, it will not go over 65 mph. Doing this prevents drivers from speeding, but it also helps reduce accident costs, fuel waste, and prolong engine life.
The actual calibration process typically takes 10 to 15 minutes, does not require any hardware adjustments, and has an immediate impact on fleet savings and safety.
If it all sounds too good to be true, check out these highlights from a North American Council for Freight Efficiency (NACFE) report:
- New trucks that optimized engine parameters beyond the original equipment manufacturer (OEM) default settings, including speed, torque limits, and idle reduction, saw an average of 5-8% fuel efficient improvements with some fleets reporting as much as a 20% improvement.
- Fleets that only optimized a few key areas such as speed and idle reduction saw fuel efficiency improvements of 3-5%.
Heavy-duty, light-duty, and medium-duty fleets across all applications can benefit from engine calibration. Vehicles run more cost-effectively and efficiently, and fleet managers and operators get greater control over costs, safety, and the bottom line.
So what’s not to like?