Proven Fuel-Efficiency Solutions For Utility Fleets
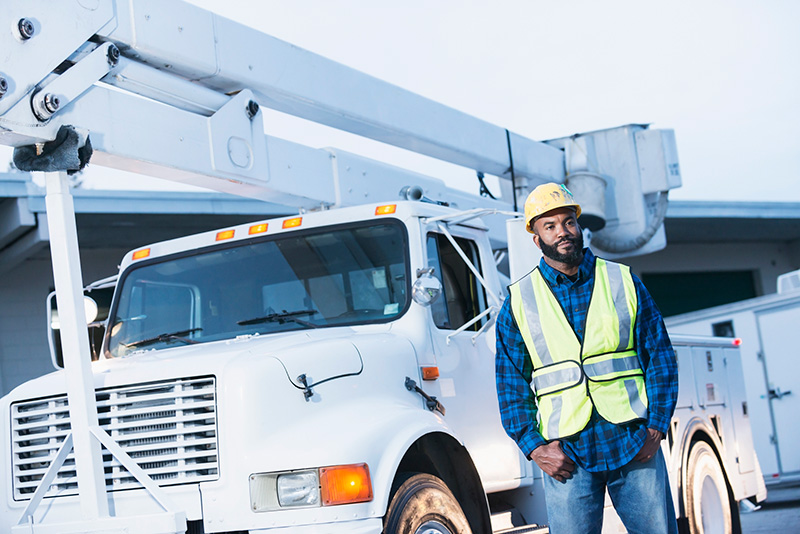
Fuel costs are one of the top operating expenses for utility fleets. For many, fuel costs can account for over half of a fleet’s operating budget. While this can be a “wake-up call” for fleet managers of any size utility fleet, it’s particularly one for larger fleets. Why? Because the larger the fleet, the faster fuel costs add up.
If you are a fleet manager, you know all too well that you can’t control the price of fuel. What you can control is how much fuel your utility fleet uses. The smart way to take control is by ensuring your technicians and trucks use fuel more efficiently.
To that end, let’s look at some proven solutions to accomplish that — solutions that will work for any type and size of utility fleet.
Make Preventative Maintenance a Top Priority
No question, keeping trucks well maintained and running efficiently and optimally gives you better fuel economy. You can attain better fuel economy by:
- Performing regular maintenance checks
- Cleaning air filters and diesel particulate filters (DPF)
- Changing engine oil
- Keeping tire pressure at recommended levels
- Aligning tires properly
For an example of what damage a little dirt can do to fuel economy, consider this…a dirty DPF increases the need for greater engine output, which can increase fuel consumption anywhere from 4.5% to 7%.
Stop Unnecessary Idling
Many utility trucks have high-powered engines that are necessary to drive air, hydraulic, and other power needs. Leaving engines running on the job site when it’s not necessary can bite into fuel economy and profitability, because engines can burn up to 0.9 gallons of fuel per hour. Plus, unnecessary idling increases engine maintenance costs and shortens engine life. Combat this by cutting the engine if running it is not necessary for the job.
Consider Fuel Efficient Equipment and Technologies
A PTO (Power Take-Off) system uses 34% more fuel on average to supply air, hydraulic, and other power needs compared to an APU (auxiliary power unit) system. Using APU-type equipment to run air, hydraulics, etc. is a sure way to reduce fuel spend. But, to get the greatest ROI, you need to choose wisely. Look for solutions that maximize fuel efficiency, such as equipment that automatically shuts off when not in use. An alternative is to select equipment that matches engine output to the load. That way, the engine is not running unnecessarily at the highest RPM and quickly burning through fuel and your fuel budget.
Lose the Weight and Rightsize Your Trucks and Equipment
According to the EPA, fuel economy is increased by 1% to 2% for every 100 pounds taken off a vehicle. Resist the urge to invest in more power than you need and evaluate whether smaller, lighter trucks that use less fuel would work for your fleet. Just make sure that your technicians can do their job just as effectively as they would with a larger, heavier truck. Additionally, consider using lightweight materials and components for truck bodies, including tools. Also, audit all onboard equipment. Any equipment that is not frequently used or is not necessary for the job should be removed from the truck. And, for those that are necessary, they should be rightsized.