Brake System Guidelines for Drivers
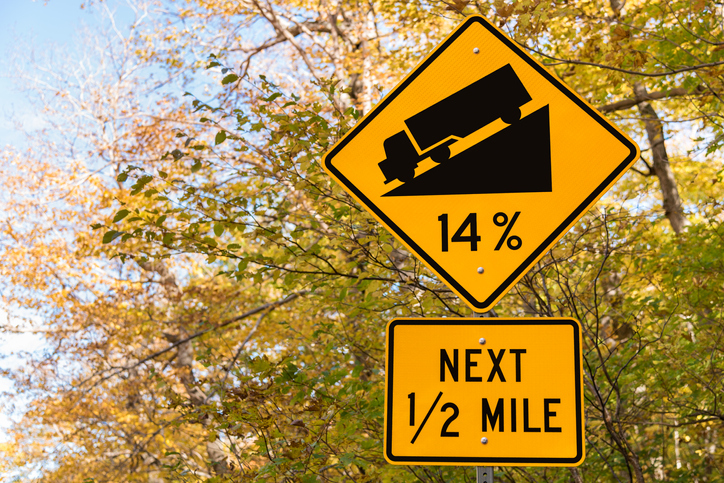
Because of their massive size and weight, the consequences can be devastating, if not deadly, when an accident involving a commercial truck happens. Truck accidents happen for various reasons, but the most common causes are speeding, distracted driving, driver fatigue, bad weather, overloading, aggressive driving, and one we will explore further here — brake issues.
According to the Department of Transportation, nearly 30 percent of all truck accidents involve brake failure, inadequate alignment, or other brake system issues. When a driver doesn’t properly apply the brakes or a malfunction in the brake system causes an accident that could have been avoided if the brakes were in proper condition, there are significant consequences. The hit to a company’s bottom line from potential legal and medical expenses, property damage, and lost employee productivity can be huge.
Brake systems are one of the most important active safety systems on a truck. Ensuring drivers know how to use and maintain brake systems properly is key to keeping everyone safe on the road.
Let’s look at essential brake use and maintenance guidelines to share with your drivers.
Brake Use
Frequent and hard braking can compromise the brake system's performance and can also increase maintenance costs by putting excessive demands on brakes and tires, springs, and shock absorbers. To get the most out of brake performance and avoid excessive maintenance costs:
- Avoid hard braking by anticipating braking needs in advance. Hard braking can potentially lock wheels and send the vehicle into a spin.
- Spread braking over the longest distance by braking early and reducing speed gradually.
- Maintain reasonable speeds and safe following distances — especially on wet/icy roads or traveling downhill.
- Apply firm pressure to the brake pedal. As you slow down, ease the pressure so that when you come to a complete stop, you should be applying minimal pressure to the pedal.
- Don’t use your engine brake or retarder (Jacobs brake) on a slippery surface. It can lock up the drive axle and cause jackknifing. Steer out of skids and minimize braking until the vehicle is under control.
- When approaching a curve, apply the brakes while the vehicle is traveling in a straight line and slow down to the point that you can apply a little power as you turn.
- Use lower gears in heavy traffic and on hills.
- Determine safety buffer. In good weather conditions and normal traffic:
- If you’re operating a 40 ft. truck under 40 mph, leave four seconds between the truck and the vehicle in front. Over 40 mph, increase the buffer to five seconds.
- For trucks over 40 ft., allow one second for every 10 feet of vehicle length and one extra second if you are traveling over 40 mph.
- If traffic is heavy or road conditions are poor — such as rain, ice, or snow — greater following distances may be required.
Brake Maintenance
Drivers are hands-on with their equipment every day, unlike maintenance technicians who typically see a vehicle for preventative maintenance or when there’s a problem. Drivers should regularly and thoroughly inspect brakes with every pre-trip inspection, including listening for air leaks, checking low air signals, and looking for component damage. Drivers should be the “eyes and ears” of maintenance technicians.
Service Brake Check
- Wait for normal air pressure, release the parking brake, and move the vehicle forward at about 5 mph. Apply the brakes firmly and note if there is any is pulling to one side or delayed stopping action.
Parking Brake Check
- Apply the parking brake only and shift into a lower gear. Gently pull against the brake by releasing the clutch to verify it holds the vehicle.
Hydraulic Brake Check
- Pump the brake pedal three times and hold for five seconds with the engine running. The pedal should not move. If the vehicle has a hydraulic brake reserve system, with the key in the off position, depress the brake pedal and listen for the reserve system electric motor turning on. Verify that the brake warning light/buzzer is off.
Air Brake Check
- For vehicles equipped with air brakes, release the parking brake and trailer air supply button and apply pressure to the foot brake for one minute. After the initial drop in pressure, the pressure loss rate should be no more than 4 psi for combination vehicles.
- Test the low-pressure warning alarm: Turn the key to the on position, rapidly depress, and release the foot brake to reduce air tank pressure. The low air pressure warning light should come on before the pressure drops below 60 psi. Continue to rapidly apply and release the service brake pedal to reduce air pressure further. The trailer air supply button (for combination vehicles) and parking brake button should pop out when the pressure falls between 20 to 40 psi. This should activate the spring brakes.
- Check the rate of air pressure buildup: While the engine is operating at 1800 RPM, the pressure should rise from 85 to 100 psi within 45 seconds in dual air systems.