Fleet Maintenance and Technology: How to Support Technicians' Skills for Your Fleets
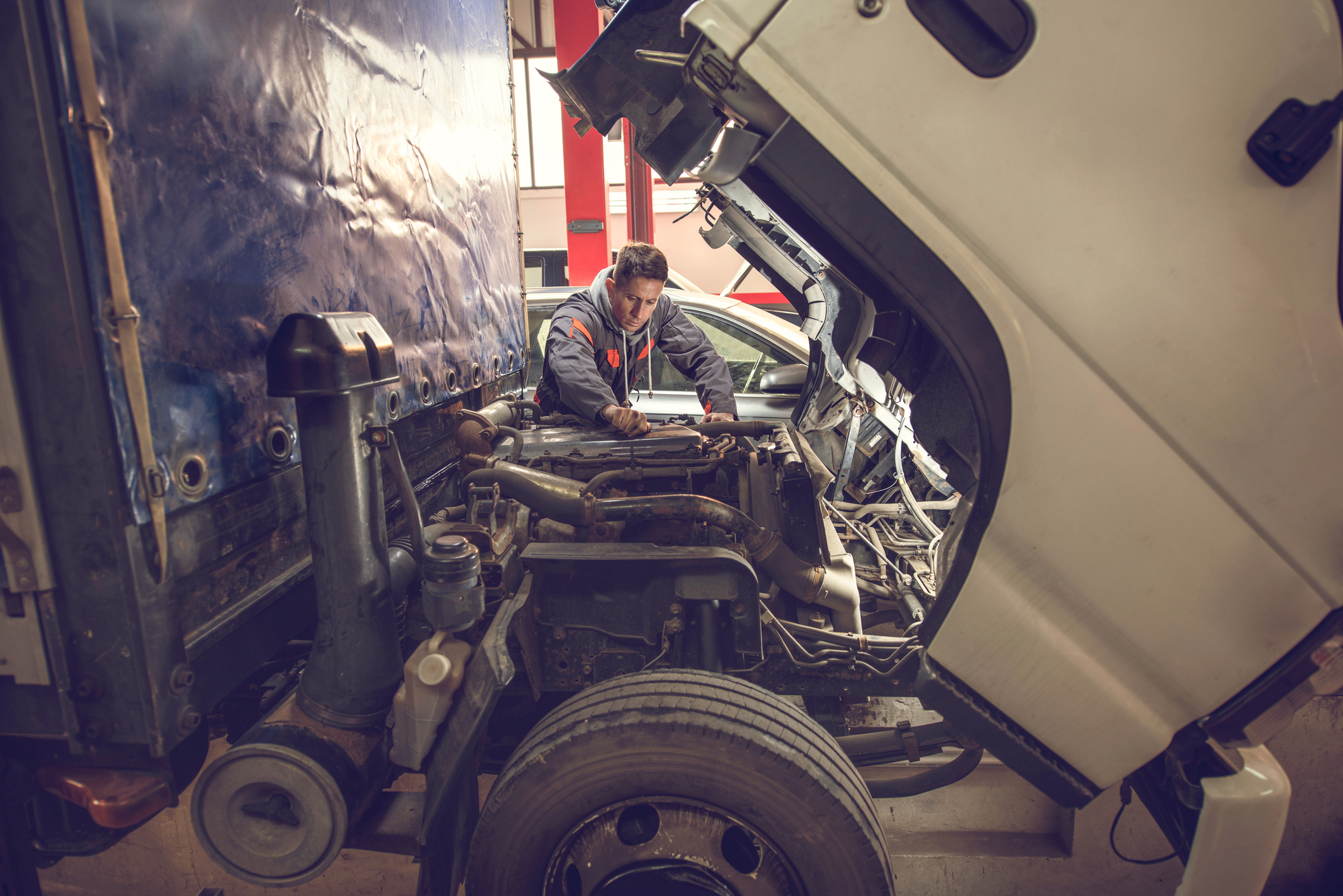
One of the most pressing issues facing fleets today is rapidly evolving technology and the challenging effect it can have on maintenance operations. In fact, according to a recent survey of maintenance professionals by Fleet Owner, three of the top five challenges for fleet maintenance operations are technology-related:
- The complexity of systems and components on new vehicles
- Finding and retaining qualified technicians
- Keeping technicians trained on the latest technologies
You could argue that technology, in this case, is like a double-edged sword. On the one hand, you have the multiple bottom line benefits that technology can provide, including safer and more efficient vehicles with vastly greater functionality. But on the other, you can have challenges that negatively impact your bottom line, including rising maintenance costs and those challenges found in the maintenance professionals survey.
The Modern Fleet Is Not Exactly the Same Old Fleet
In the not too distant past, fleets were typically comprised of vehicles of the same type and class. Today, many fleets operate a wide range of vehicles that are powered by fuels, electricity, and hybrid systems. They are also equipped with sophisticated components, sensors, and electronics systems that are expensive to maintain and repair. For fleets to survive and thrive, technicians must not only be thoroughly knowledgeable of “old school” components, but also of “new school” computer systems, software programs, alerts codes, telematics components, sensors, and video technology, to name a few.
These “new school” technologies and emerging technologies that are rapidly coming down the pipe add even more pressure to the already stressed technician workforce. The Bureau of Labor Statistics estimates that by 2022 there will be a need for 67,000 technicians to replace retiring workers along with the additional 75,000 technicians that will be needed to meet market demand.
It is now more important than ever for fleets to put steps in place that ensure technicians are qualified to maintain and repair vehicles and the various technologies with which they are equipped. One way to achieve this is to partner with a service provider. This will alleviate the time-consuming burden of finding technicians. The other is retaining and training technicians to help ensure both their long-term success and that of the fleet.
Let’s look at five key steps to help you with retaining and training your fleet.
1. Provide Ongoing Technology Training:
The most important job is to keep technicians up to speed with training on new technologies and new types of vehicles. This will ensure that your technicians keep your fleet running efficiently.
Best practices to consider include:
- Building a roster of training partners, such as fleet associations, colleges, and trade schools
- Taking advantage of training programs and manufacturer-provided courses
- Using computer, video-based training, virtual reality, and augmented reality as training tools
- Recruiting entry-level candidates that you can train-up and who fit your fleet’s culture
2. Make Priorities Known:
Identifying what is most important will help guide technicians on those tasks on which they need to be focused Knowing what is expected provides better time management and alleviates the frustration from time spent on the wrong task. Frustration on the job is never good and could lead to a qualified technician, in whom you have invested time and money, leaving your fleet to work elsewhere.
3. Set Goals:
Layout clear career paths and professional goals for technicians, to ensure they are continuing to develop in their roles and career. Items to consider should be those that help improve both the employee and your fleet operations, such as completing training courses, taking leadership classes, and improving various job efficiencies.
4. Compensate Fairly:
Money isn’t everything, but it sure helps in keeping technicians productive and focused on developing their skills. Make pay comparable with averages in your area and offer incentives when goals are met, or when training courses are completed.
5. Provide Career Advancement Training:
The more skilled your technicians, the more valuable they are to your company. Career advancement training can help a technician determine the best career path to take and lets you know the skills and training necessary for that path. A technician thinking in terms of a career with you and not just a job, will develop loyalty and be more likely to stay onboard with you for career advancement opportunities.
Need more best practices around fleet management, download our latest guide.