Determining the Optimal Vehicle Replacement Cycle
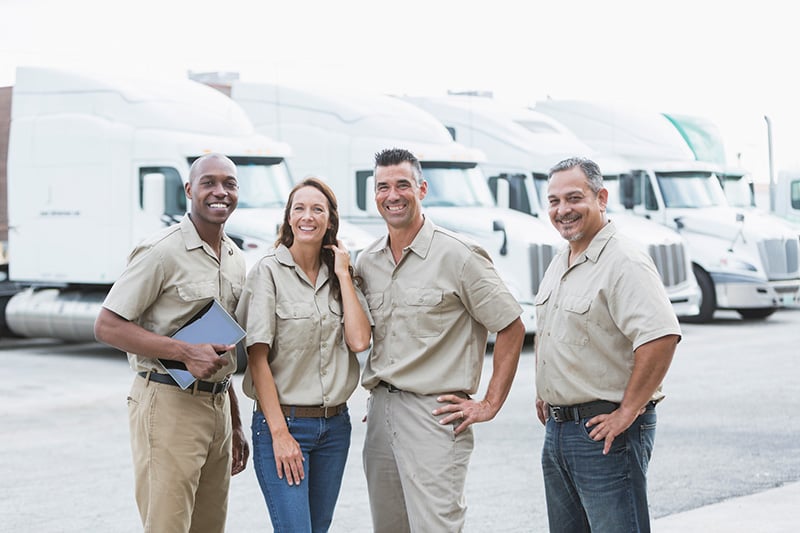
Fleet managers have the responsibility of staying focused on the job at hand and the responsibility of planning and prioritizing future fleet and company needs. Fuel planning, preventative maintenance scheduling, budgetary projections, and determining the optimal vehicle replacement cycle are just a few of those.
Arguably, all these responsibilities are equally important, but one that is not always prioritized is determining the optimal vehicle replacement cycle. For various reasons, this responsibility is often approached with a reactive “wait and see.” This approach should be avoided because it can prove to be expensive in terms of maintenance costs, fuel costs, and downtime.
Good Things Don’t Necessarily Come to Those Who Wait
Playing a waiting game until vehicles are driven into the ground is not the vehicle replacement route that should be taken. Replacing a vehicle while you can still maximize its resale value and before maintenance costs and downtime are on a positive trend is a more desirable alternative.
The methods used to accomplish this alternative vary by fleet; however, being proactive and implementing a replacement cycle for each vehicle or vehicle segment is a workable solution that can minimize downtime and lower operating costs. Additionally, it can make a driver feel more confident behind the wheel of a recent model vehicle that’s outfitted with the latest safety and technology features.
What actions should be taken to determine the optimal vehicle replacement cycle? Let’s look at five key best practices and considerations.
1. Determine Company Needs
Evaluating vehicles and conducting a fleet analysis is the foundation for any vehicle replacement cycle. Knowing what you have before you begin to develop or alter a vehicle replacement cycle will help ensure sound results. Some questions to consider, include:
- What is the optimal number of vehicles needed to support the fleet?
- Are there vehicles that aren’t fully utilized, have excessive downtime, or are sitting idle?
- What are the tasks of each vehicle?
- Do vehicles sync with operational needs and business requirements and are these vehicles the optimal type, class, and size?
- Are there vehicles that are no longer cost-effective to operate or are not fulfilling their purpose?
- Can a vehicle be replaced with a lighter, more fuel-efficient vehicle?
2. Take a Hard Look at Data
With advances in telematics, fleet managers have access to more data than ever before, which means there’s opportunity for better decision-making. With this collected data, fleet managers gain greater transparency into fleet operations, including maintenance records, vehicle downtime, and fuel expenditures. With a thorough data analysis, fleet managers can spot red flags and make necessary improvements, and this data can be used as building blocks for developing a solid vehicle replacement cycle.
3. Don’t Forget the Basics
While vehicle replacement cycles vary by fleet, there are basic factors to developing a cycle that can be applied to all fleets. These factors include the vehicle model, year, total miles, overall vehicle condition, cost per mile, and repair costs over a fixed time period . And, it is critical to consider them all. Considering only a single factor for vehicle replacement can be risky and here’s why.
Perhaps two vehicles are the same model, year, type, and have relatively the same mileage. One of the vehicles carries specialized equipment and is used to power that equipment. This increases wear and tear and also increases fuel consumption. Comparison to a like vehicle, without specialized equipment, will deliver inaccurate information when developing a replacement cycle.
4. Specialization
Since vehicles outfitted with specialized equipment typically involve a larger upfront investment, they are usually kept in service for longer periods of time. When considering a replacement vehicle with the same specialized equipment, one is likely looking at an investment that is just as large, if not larger, than the investment made for the vehicle being replaced. These are considerations that are important in determining the “total cost of ownership” of a vehicle.
5. Used Vehicle Cycles and Demand
The best time to sell a vehicle is typically between spring and fall, but this can be affected by the demand for the type of vehicle being sold . It may be advantageous to adjust cycling seasonality to maximize the resale value and get the best price.
Bottom Line
There is no one-size-fits-all strategy for developing an optimal vehicle replacement cycle. However, taking the time to develop a sound strategy, using the best practices and considerations applicable to the fleet, can have a positive impact and can ensure a more cost-effective fleet on the road.
Remember that your fleet represents your company. Rusty vehicles, inferior paint, and body damage are poor representations, so make sure both your vehicles and your company shine.
Want to test your knowledge on more best practices for your fleet? Check out our interactive quizzes to see how well you score.