Creating an Effective Maintenance Program
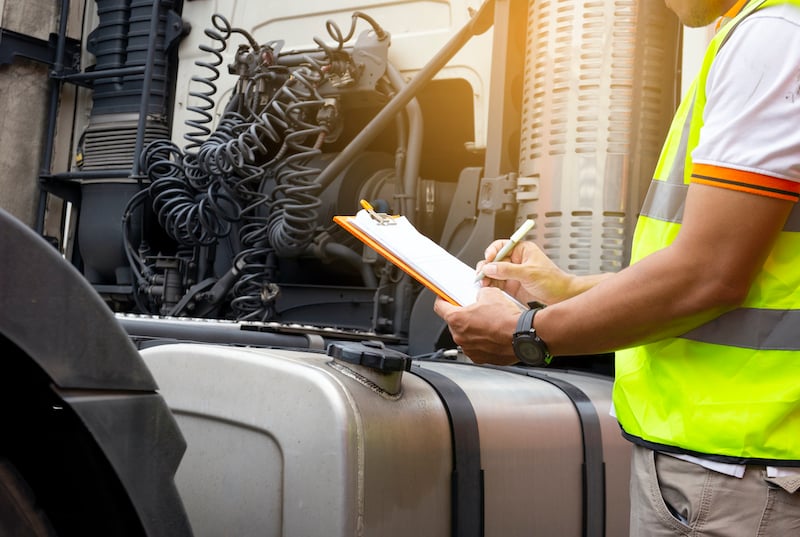
Keeping fleet vehicles maintained adequately is one of the most critical aspects of fleet management. It is also key to growth and profitability. Just one vehicle “in the shop” can cause all kinds of problems that lead to lost profits, including:
- Delayed pickups, deliveries, and on-site job completions
- Decreased fuel efficiency
- Increased accident risk, breakdowns, and downtime
Five vital objectives for every fleet manager are ensuring driver/vehicle safety, keeping vehicles on the road, reducing vehicle and overall operating costs, maintaining vehicle resale value, and ensuring compliance with regulations. A fleet maintenance program is a sure-fire way to meet all these objectives.
To that end, let’s take a look at four steps for creating an effective program — one that will keep your fleet safely moving forward and help your business and profits grow.
1. Know Your Vehicles
Knowing your fleet vehicles inside and out is key to laying the groundwork for your program. This includes:
- Vehicle metrics, including types of vehicles, age, fuel usage, maintenance history, mileage, and hours of operation
- Drivers and their certifications
- Routes traveled
- Regulations that affect fleet operations
- Current maintenance costs
- Vehicle downtime due to repairs, maintenance, or violations
When laying the groundwork, you also need to determine who is responsible for the maintenance service. For example, are services provided by an on-site service department or outsourced? Additionally, you need a streamlined process for scheduling service and ordering parts to ensure vehicles are available.
Depending on your fleet's size, you may want to consider fleet management software to track and update vehicle information. The software can also define triggers and issue alerts when a vehicle is due for a maintenance interval. Keeping track of information and schedules can be a time-consuming process. A software solution can reduce time and labor spent on these tasks, allowing you more time to focus on core processes that promote business growth.
2. Develop a Maintenance Checklist
Your checklist should be a thorough list of what items needed to check when vehicles are serviced, including:
- Engine and transmission mounts
- Oil and filters
- Drive shafts, CV joints, belts, and hoses
- Cooling and fuel systems
- Electrical components
- Brake system
- Steering and suspension
- Tires, wheels, and rims
- Exhaust system
- Windshield wipers and fluid
- Undercarriage and frame
- Seatbelts
- Seats
- Lighting
- Glass
- Leaks
- Added components
You may want to consider routine fluid analysis on your checklist — specifically oil, coolant, and diesel fuel. Fluid analysis gives you visibility into asset performance and component health and helps you realize benefits that boost productivity and profitability, such as avoiding costly failures and shortened repair times.
Full fluid testing and comprehensive reporting from a reputable provider can help spot problem areas.
Examples of testing to find these potential problem areas follow:
- Oil sampling and analysis can check for contaminants that can hamper performance and cause engine damage.
- Coolant sampling can determine if your coolant has the right chemical balance for maximum protection.
- Diesel fuel sampling can check for fuel quality since inferior quality can affect performance and drive up maintenance and operating costs.
3. Build a Preventative Maintenance Schedule
Every vehicle is different, so before building your schedule, you must first know each vehicle's specific needs. Some vehicles may have components that need other services than those that rely on mileage or hours driven/operated. Equipment added, such as custom power units or cranes, will need to have its maintenance schedule or inspection. Also, ensure that if an on-site service department handles maintenance, that available labor aligns with maintenance needs.
With the information on each vehicle and components — including any previous history — you can create a 12-month maintenance schedule for each vehicle that triggers the appropriate times (again, consider fleet management software to help with scheduling and alerts). Other factors to consider when creating your schedule include:
- Number of drivers that use the vehicle
- If the vehicle operates in rough terrain or off-road
- Climate conditions
- Whether the vehicle idles and sits in traffic for long periods
4. Get Your Team On Board
Make sure you communicate the schedule to the necessary individuals. Gather feedback that may affect the schedule and will help your service team plan for labor needs.
Trained drivers know their vehicles and can pick up subtle signs during operation that technicians making routine inspections may not pick up on. Having a driver inspection and reporting system that requires drivers to take note of and report any concerns they have before, during, and after vehicle operation can catch little problems before they become bigger ones.