Best Practices for Successful Aircraft Equipment Operations
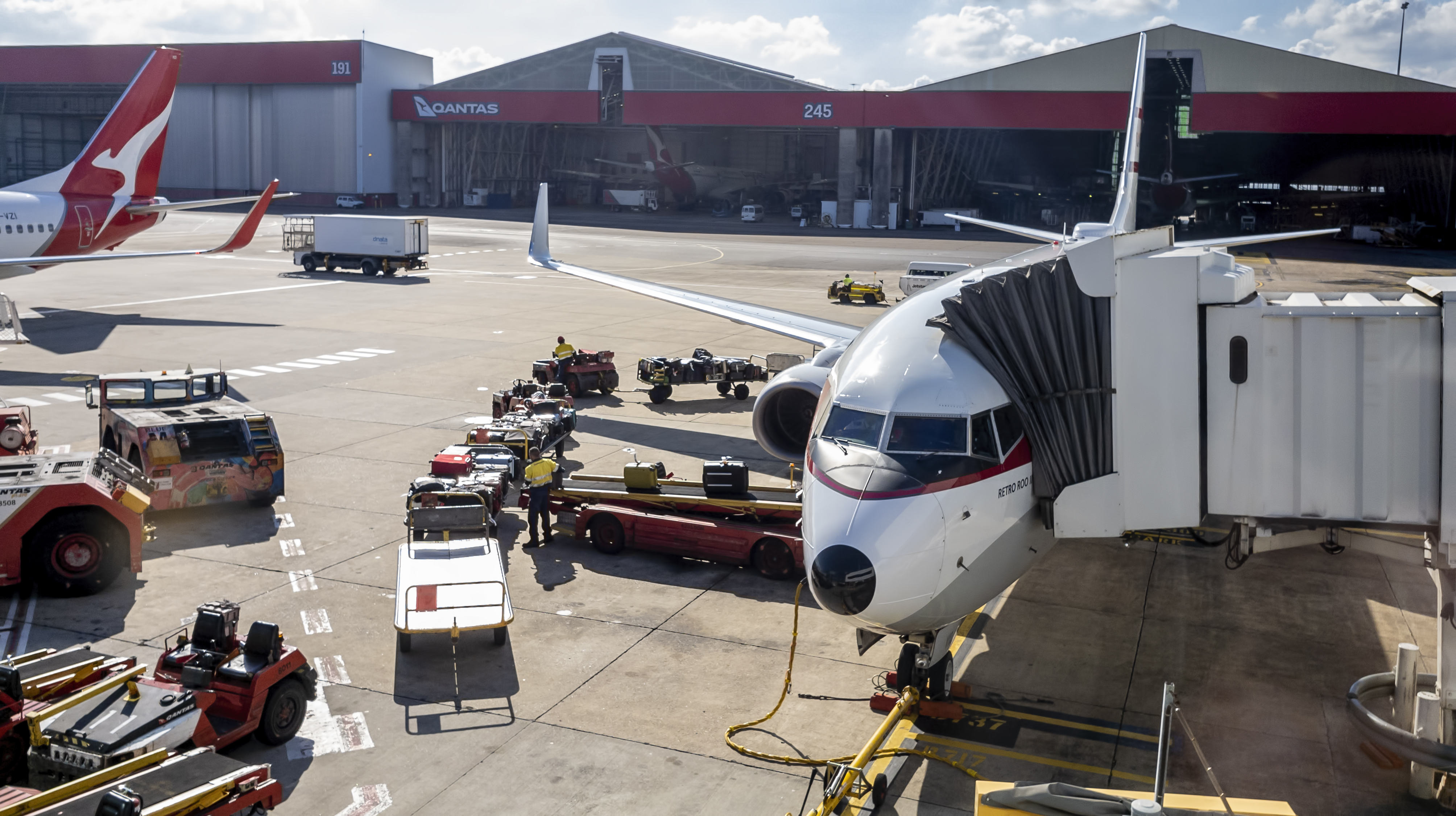
To keep airport facilities running efficiently and safely, ground support crew managers must stay on top of the hundreds of moving parts that are necessary for the successful operations of ground support equipment (GSE). This can include anything from managing ground support crew, to directing GSE movement, to procuring, managing, and monitoring fuel for vehicles and equipment, such as generators.
Airports can be a hectic place and can be especially hectic on the flight line where aircraft are loaded, offloaded, and serviced. After an aircraft lands, the ground support crew and GSE must complete services that support the safe operations of the aircraft before that aircraft takes off again — and complete services safely and in the shortest time possible
To ensure the success of aircraft equipment operations and ground handling operations, adopting best practices is a strategy to meet that goal. To that end, let’s take a look at four best practices to consider to help ensure GSE operations are safe, on schedule, and on budget.
1. Upgrade GSE for Greater Efficiency
With wear and tear, GSE can become inoperative, less efficient, and more expensive to operate. This is particularly true for gasoline-powered GSE. Choosing electric-powered or diesel-powered equipment can provide substantial cost savings from the get-go and help reduce fuel consumption considerably — saving thousands of dollars which can be put to use for improvements in other operational areas.
Additionally, using electric equipment can prevent unnecessary idling time. This helps eliminate harmful CO2 emissions on the flight line, which is healthier for both the environment and the ground crew who operate the equipment.
2. Make Training Comprehensive and Continuous
GSE is only as efficient as the ground crew who work with it every day. To keep operations safe and running efficiently, continuous training for ground crew is key to creating a safety-first culture and key to equipping the ground crew for success.
For training best practices there are two key benefits to keep in mind. The first is should an incident occur, training records will show due diligence on the company’s part. The second is that training and opportunity improve employee retention. Learning new skills keeps employees engaged. Just make sure to incentivize good performance, which is a plus for keeping the best employees and increasing the standards of airport operations.
3. Utilize GSE Fleet Telematics
Just as telematics provides commercial fleet managers insight into what’s happening with vehicles at any time, telematics provides ground support crew managers insight into what’s happening with equipment and ground handling operations. This insight allows for faster, smarter, and data-driven decision-making that improves ground handling operations and overall airport operations.
Telematics can help identify opportunities for cost savings, streamline operations, minimize downtime, and allow ground crew managers to schedule preventative maintenance, which helps eliminate costly unscheduled repairs and vehicle and equipment downtime.
Additionally, telematics can promote the safety of ground crew with monitoring capabilities that help ground crew managers stay on top of their crew’s operating behavior — allowing managers to immediately correct any risky behaviors with training or coaching.
4. Partner With the Most Qualified Bulk Fuel Providers
There is no shortage of bulk fuel providers for airports. Knowing the qualifications, services, and solutions to look for is key to keeping ground operations running cost-effectively, efficiently, and safely. Look for a provider with:
- A proven track record of bulk fuel delivery, management, and monitoring for airport facilities and ground vehicles.
- A wide range of solutions to meet fuel needs reliably and cost-effectively.
- Guaranteed fuel supply. Make sure the provider has multiple sources. A single-source provider can be vulnerable to fuel shortages and high prices.
- Advanced equipment, information systems, fuel management platform, and technology to create safe, cost-effective, and reliable methods for bulk fuel purchasing, inventory management, fuel use tracking, fuel quality testing, and environmental compliance.
- 24/7/365 availability.